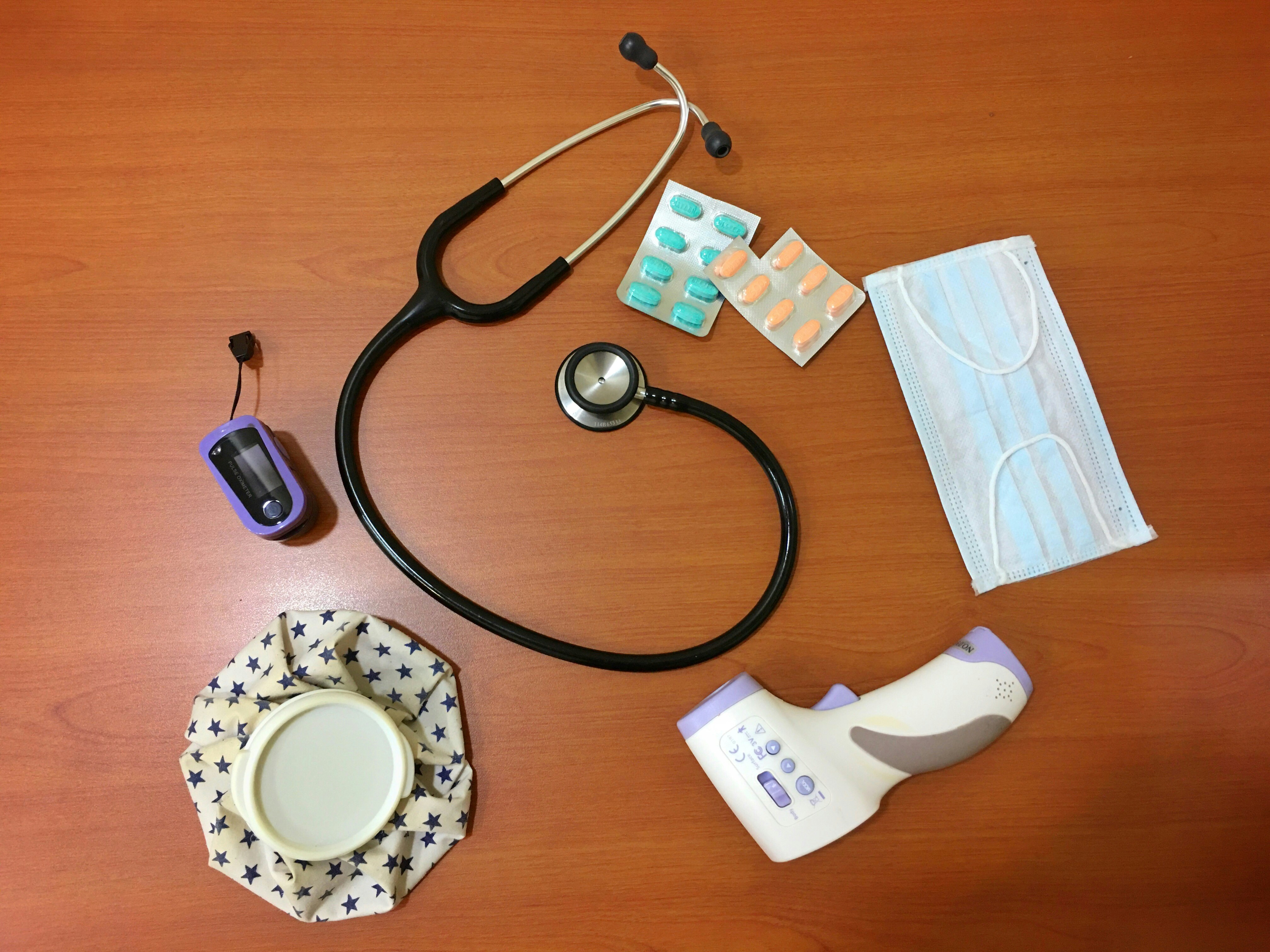
Building a Foundation for MedTech Success: Design & Development
Part 3: Design & Development
Once your team has demonstrated product feasibility, it’s time to double down on building a device that is safe, effective, and regulatory-ready. The design and development phase is where your device begins to take its final shape: technically, visually, and functionally. During this phase, you’ll need to apply design controls, plan for usability testing, align with your regulatory strategy, and prepare for manufacturing handoff. A well-structured approach here pays dividends down the line, especially when it comes time to submit to the FDA or scale production.
This guide breaks down the key activities and tools that help teams manage this phase efficiently and compliantly.
Design Controls & Documentation
Design controls ensure your product development process translates user needs into actionable requirements and later into tangible outputs. The FDA mandates this structure under 21 CFR 820.30. ISO 13485 has similar standards.
The flow generally looks like:
User Needs → Design Inputs → Design Outputs → Verification & Validation
Each phase should be traceable and documented. Tools like Arena PLM and Greenlight Guru help manage this workflow, while Qualio ensures that your documentation stays compliant and audit-ready.
Human Factors & Usability Engineering
If your device has a user interface – digital (app, software) or physical (display, wearable) – you’ll need to integrate Human Factors Engineering (HFE) into the design process. The FDA’s Human Factors Guidance outlines how to reduce user-related risk:
- Formative testing: Gather early user feedback to guide design changes
- Summative testing: Validate that the final product can be used safely and effectively
UserWise and Emergo by UL specialize in these usability assessments. Human factors work isn’t just a checkbox: it can be the difference between FDA clearance or rejection, usually due to preventable errors.
Ongoing Risk Management
FMEA and Hazard Analyses should evolve alongside your product. Risk mitigation strategies are tied directly to design decisions and will influence the eventual V&V plans you follow through.
Tools such as OpenRegulatory’s FMEA template and Medical Device HQ’s Hazard Traceability Matrix make it easier to update and track risk documentation. Your risk profile must align with ISO 14971 standards and should remain a living document through clinical and commercial launch.
Design Transfer Planning
Eventually, the design must leave the R&D lab and enter manufacturing. Planning for design transfer means preparing specifications, bills of materials, SOPs, and inspection procedures. The FDA requires this under 21 CFR 820.30(h), and ISO 13485 reinforces it in Clause 7.3.8.
Greenlight Guru and MasterControl QMS can support this handoff. Ensuring a clean transfer helps avoid production errors and regulatory missteps later.
Bill of Materials (BOM) & Quality Controls
Your BOM should detail everything needed to manufacture and assemble your device—from raw materials to final components. Platforms like Katana or Asana’s BOM template help teams manage this complexity and collaborate with contract manufacturers.
You’ll also need to implement quality controls to ensure that what you produce matches what was designed. Templates from Qflow or HashMicro can guide testing protocols and inspection criteria.
Final Thoughts
The design and development phase transforms early ideas into a production-ready device. With structured documentation, user-informed design, and proactive risk management, startups can avoid last-minute surprises and build a product that’s ready for FDA review—and the real world. Treat this stage as the foundation for your next big milestone: verification, validation, and submission.